Overstock and obsolescence are synonymous with hidden costs; they are detrimental to the company’s cash flow. However, some companies are faced with recurring overstock or out-of-stock situations. What are the reasons for this? How can they be avoided? What management policy ensures the best stock quantity is available? Answers.
Excess stocks and obsolescence: where do they come from?
Is your company running out of stock? This can result from various factors, either individually or in combination.
1. Batch production
While this practice saves on manufacturing, purchasing and transport costs, batch production can lead to excess stock, which ties up cash, takes up valuable storage space and requires handling. It is only possible to produce or buy batches of 1000 products if the company sells 30 per year. This would only create excess stock, which is likely to become obsolete…
2. Safety stocks
By definition, the safety stock is surplus: it is specially provided for, in addition, to cope with unforeseen events. This gives companies leeway to deal with possible shortages, long supply times or unexpected demand behaviour. But beware. Building up a safety stock is a balancing act, as it must be constantly monitored to ensure that the store is neither too high nor too low.
3. Unsold goods
Products that do not sell remain, by definition, “in the hands” of the company. They then become surplus stock and then obsolete stock…
4. Unreliability or lack of forecasting
A company that produces or orders according to habits without looking at demand movements is risking creating unnecessary stock (or being out of stock). A good sales forecast, as reliable as possible, reduces costs and improves the service rate. In this way, demand is considered and measured.
5. Order cancellations
When orders are cancelled and production has already started, companies must manage an overstock of items. These items clutter the warehouse shelves and are harder to sell.
6. Marketing optimism
The marketing department may think a product will sell well… when it will not. Launching a product or its promotional campaign phase can lead to a potentially large overstock. Good communication and collaboration between departments can help to avoid this situation.
7. The product life cycle
Finally, overstock can result from poor management of a product’s end-of-life, difficulty in disposing of its stocks or its replacement by another range.
Beyond these 7 factors, there are 2 examples of surplus (but not obsolete!) stocks which, this time, are virtuous. Firstly: anticipation stock. Some companies with solid seasonality, for example, with a peak in sales at Christmas, anticipate seasonal demand by producing in advance at another time of the year. This practice avoids being in a risk position just before the peak, makes industrial savings and avoids overtime. Secondly: the stock of materials before an increase. In the current inflationary context, some companies order in mass to stock up on materials at the current market price to anticipate the price increase. These two examples are the result of an anticipatory S&OP strategy. The excess stock is controlled and is beneficial to the company.
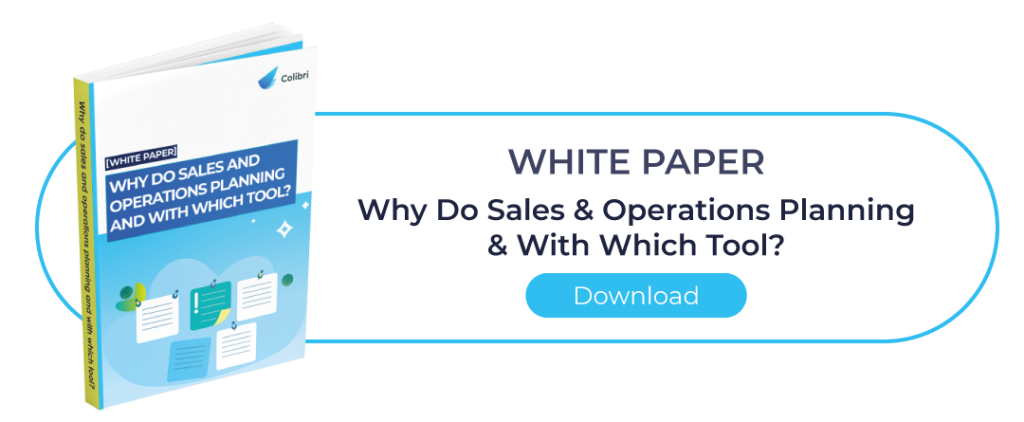
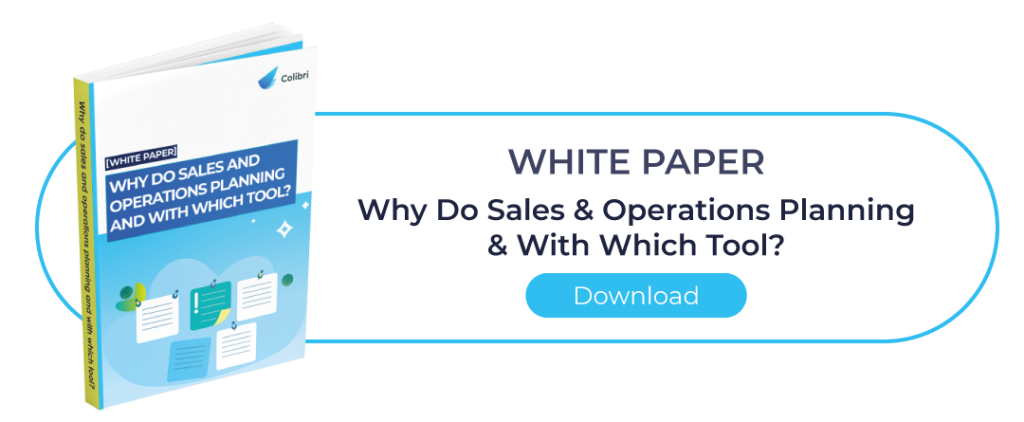
Excess stock, obsolescence, and consequences for the company
Excess stock is often a problem for a company. Firstly, because it clogs up the warehouse. This leads to additional costs for storage and handling.
In addition, overstock ties up cash. And this money can be permanently lost if the product becomes obsolete! The company can then face significant financial losses…
Finally, excess inventory limits the company’s ability to invest. This is because part of the cash flow is blocked until the products are sold.
How to avoid overstocking and obsolescence?
1. Measuring the rate of excess stock and obsolescence
The first thing to do is to measure excess inventory and obsolescence. Take a close look at the amount of stock you have for each product and check which of these references are no longer usable, mainly because of obsolescence.
2. Rationalise stocks to avoid overstocking and obsolescence
Are you afraid of running out of cash or tying up too much? In this case, the best reflex is rationalising by getting out of the effect. Now that you have measured your rate of excess stock and obsolescence, you can make rational and informed decisions to manage your stocks more effectively.
Make sure you analyse and update your stock levels as regularly as possible. This allows you to react in time and take the right decisions to avoid overstocking and potentially selling off or, even worse, destroying products…
3. Managing stocks with S&OP
S&OP positively impacts by enabling the teams to control the planning load. The Sales and Operations Planning strategy is steered over 12 to 24 months in the correct orders of magnitude.
The teams benefit from a shared global vision, which makes stock management more relevant. This also results in more reliable forecasts. The company can then implement a more efficient strategy and, by extension, better control service rates, stock levels, workloads, capacities, and supply flows.
In addition, a well-managed stock improves employees’ working conditions. Teams work more serenely and less in a hurry, enhancing their productivity. They can concentrate on high-value-added tasks, and the whole company wins!
Finally, S&OP has the advantage of facilitating the management of the company’s turnover and margins. Associated with the right tool, an optimised S&OP process helps the teams and the company to gain serenity and performance. It makes strategic decisions more accessible and more objective. In a world in perpetual motion, this represents a real competitive advantage.
To optimise your inventory management, adopt the COLIBRI tool. COLIBRI is a native cloud-based S&OP solution that allows you to make the right decisions and gain agility at all levels. Take advantage of all the benefits of S&OP today. Ask for your demo!
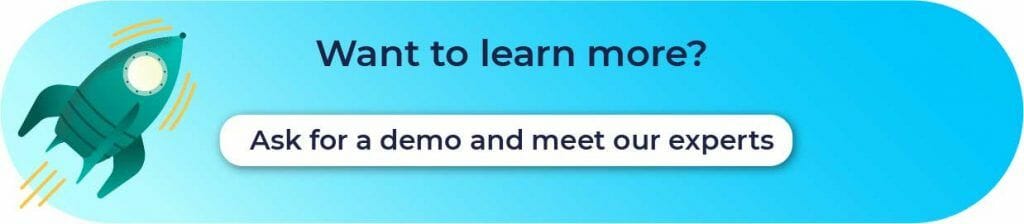
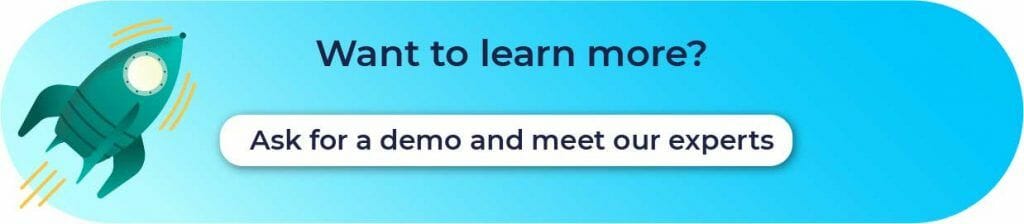